In the realm of manufacturing, the advent of 4-axis and 5-axis CNC machining has ushered in a new era of precision and efficiency. These advanced machining techniques play a pivotal role in various industries, ensuring accuracy and intricate detailing that were once thought impossible. Today, we delve into seven transformative applications of 4-axis and 5-axis CNC machining, showcasing its impact across diverse sectors.
1. Aerospace: Navigating the Skies with High Precision Machining in India
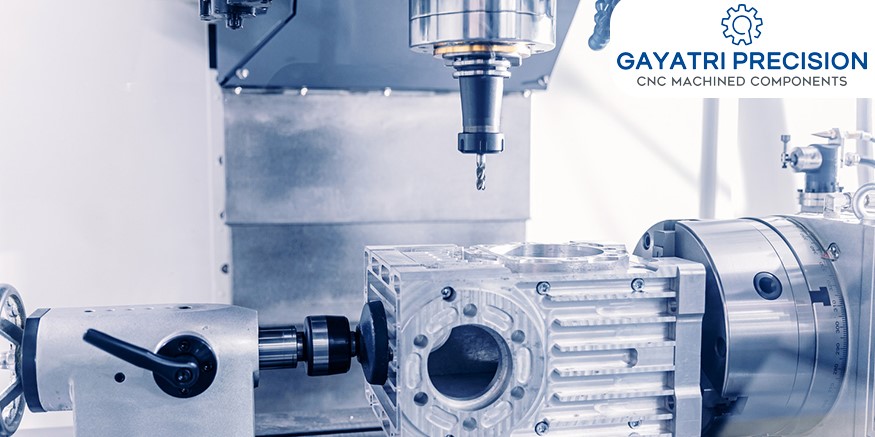
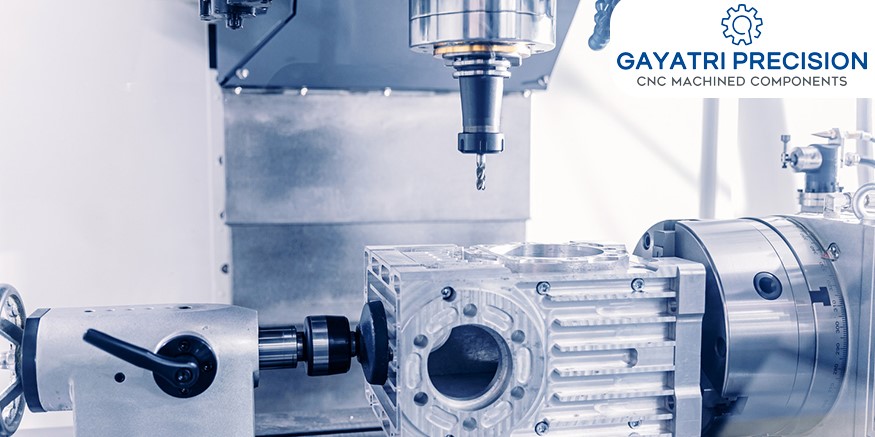
When it comes to aerospace engineering, precision is non-negotiable. 4-axis and 5-axis CNC machining play a pivotal role in crafting intricate components for aircraft and spacecraft.
From lightweight structural parts to complex engine components, the technology ensures high precision machining in India and around the world. The ability to maneuver on multiple axes allows for the creation of intricate and aerodynamically efficient parts, contributing to the overall performance and safety of aerospace vehicles.
2. Automobile: Driving Precision Engineering
In the automotive industry, precision is synonymous with safety and performance. 4-axis and 5-axis CNC machining enable the production of intricate automotive components with unparalleled accuracy.
From engine parts to transmission components, these machining techniques ensure that every piece fits seamlessly, enhancing overall efficiency and reliability on the road.
3. Fire and Safety: Precision in Protection
Precision CNC machining is a crucial player in the development of components for fire and safety equipment. Whether it is intricately designed parts for firefighting gear or components in safety systems, the precision achieved through 4-axis and 5-axis machining ensures that every piece functions flawlessly, contributing to the reliability of life-saving equipment.
4. Oil and Gas: Precision in Extreme Environments
The oil and gas industry operates in challenging environments that demand components capable of withstanding extreme conditions. Precision CNC machining is instrumental in creating robust and durable parts for drilling equipment, pipelines, and valves. The ability to produce complex components with tight tolerances ensures that these critical parts can endure the harsh environments of oil and gas operations.
5. Instrumentation: Harmonizing Precision in Measurement
In the world of instrumentation, accuracy is paramount. Precision CNC machining plays a pivotal role in crafting intricate components for measuring devices, sensors, and testing equipment.
The multi-axis capabilities allow for the creation of precise and intricate parts, contributing to the reliability and accuracy of various instruments across industries.
6. Medical: Precision for Life-Saving Innovations
The medical field demands the highest level of precision, and 4-axis and 5-axis CNC machining delivers just that. From surgical instruments to implantable devices, these machining techniques contribute to the advancement of medical technology. The ability to manufacture intricate and customized components ensures that medical devices meet the stringent standards required for patient care.
7. Water Treatment: Precision for Sustainable Solutions
The water treatment industry relies on precision engineering to ensure the efficiency and longevity of its equipment. 4-axis and 5-axis CNC machining contribute to the production of precise components for pumps, valves, and filtration systems. This precision ensures the reliability and effectiveness of water treatment processes, which is crucial for providing clean and safe water.
Diversifying Perspectives: Exploring Further Applications of 4-Axis and 5-Axis CNC Machining
Let us look at the two noteworthy applications, compressors and control valves, that further exemplify the versatility and impact of these advanced machining techniques.
Compressors: Powering Precision in Compression Technology
Compressors are pivotal in a multitude of industries, playing a crucial role in increasing the pressure of a gas to propel it through pipelines or power various mechanical processes.
4-axis and 5-axis CNC machining contributes significantly to the manufacturing of compressor components. The precision achieved through these machining techniques ensures seamless functionality, optimal performance, and enhanced energy efficiency in compressors.
From intricate rotor designs to precise housing components, CNC machining plays a key role in creating compressors that meet the demanding requirements of diverse industrial applications.
Control Valves: Precision in Regulating Flow
Control valves are essential for managing fluid flow within pipelines and systems, and regulating the rate, pressure, and direction of fluid flow. Achieving precision in these valves is essential for maintaining optimal control over fluid dynamics.
4-axis and 5-axis CNC machining bring their expertise to the table, allowing for the creation of intricate and precisely calibrated control valve components. The ability to manufacture components with tight tolerances ensures that these valves operate with the utmost accuracy, contributing to the efficiency and reliability of fluid control systems.
In the fast-paced world of high-precision machining in India and beyond, the applications of 4-axis and 5-axis CNC machining are truly transformative. From soaring the skies in aerospace to enhancing safety in fire and rescue operations, these machining techniques are at the forefront of innovation.
Thus, these transformative applications explored here showcase the adaptability and impact of 4-axis and 5-axis CNC machining, marking a paradigm shift in the world of manufacturing.
In the pursuit of excellence, precision engineering remains a cornerstone, and the contributions of Gayatri Precision Metals echo this sentiment. Our commitment to advancing CNC machining technology underscores the transformative capabilities discussed herein, reaffirming the significance of precision in the ever-advancing industrial landscape
As we navigate the complexities of manufacturing, precision remains the driving force, shaping a world where every component counts and every axis matters.